

And it has gone from an environmental nightmare to a dream - no longer requiring a hazardous carrier and needing only water as a coolant. Still used for tackling advanced materials, the process is now far from slow, increasing productivity up to five fold as compared to conventional hard-material-cutting methods. The passing of 47 years has done wonders for ultrasonic cutting technology. While AM was impressed by the new technology's capabilities, editors didn't offer glowing reviews because, besides the hazards of the kerosene medium, the process was slow. That technology was ultrasonic machining, which, at the time, was performed by ultrasonically agitating grinding abrasives in a kerosene "carrier" that transported them to the workzone. In 1955, AMERICAN MACHINIST editors reported on a technology that was "one practical remedy" to machining new, hard materials.
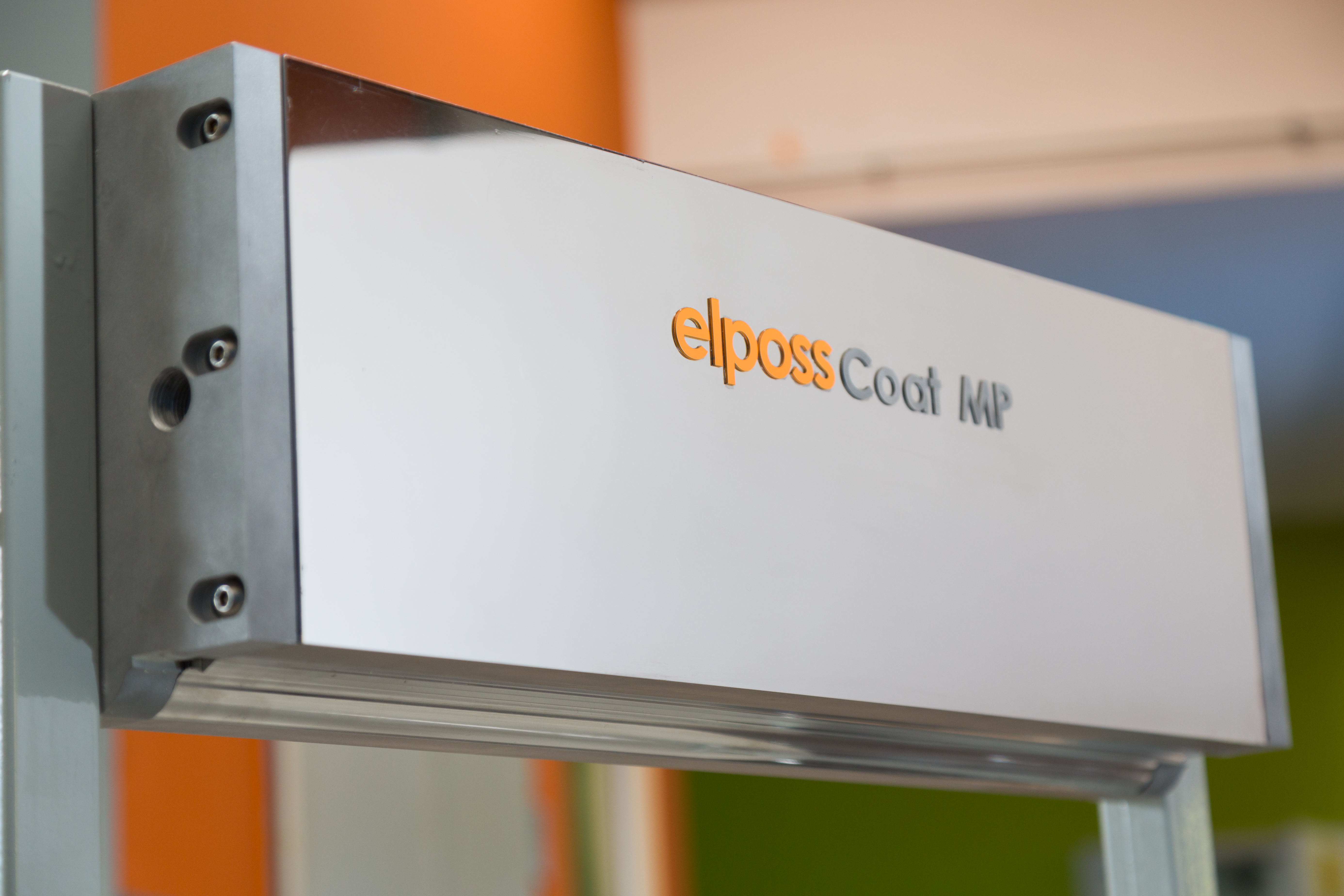
The DMS Ultrasonic Series system machines brittle materials up to 5 faster than conventional hard-material-cutting methods. Ultrasonic cutting matures into a viable machining process.
